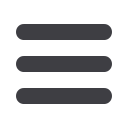
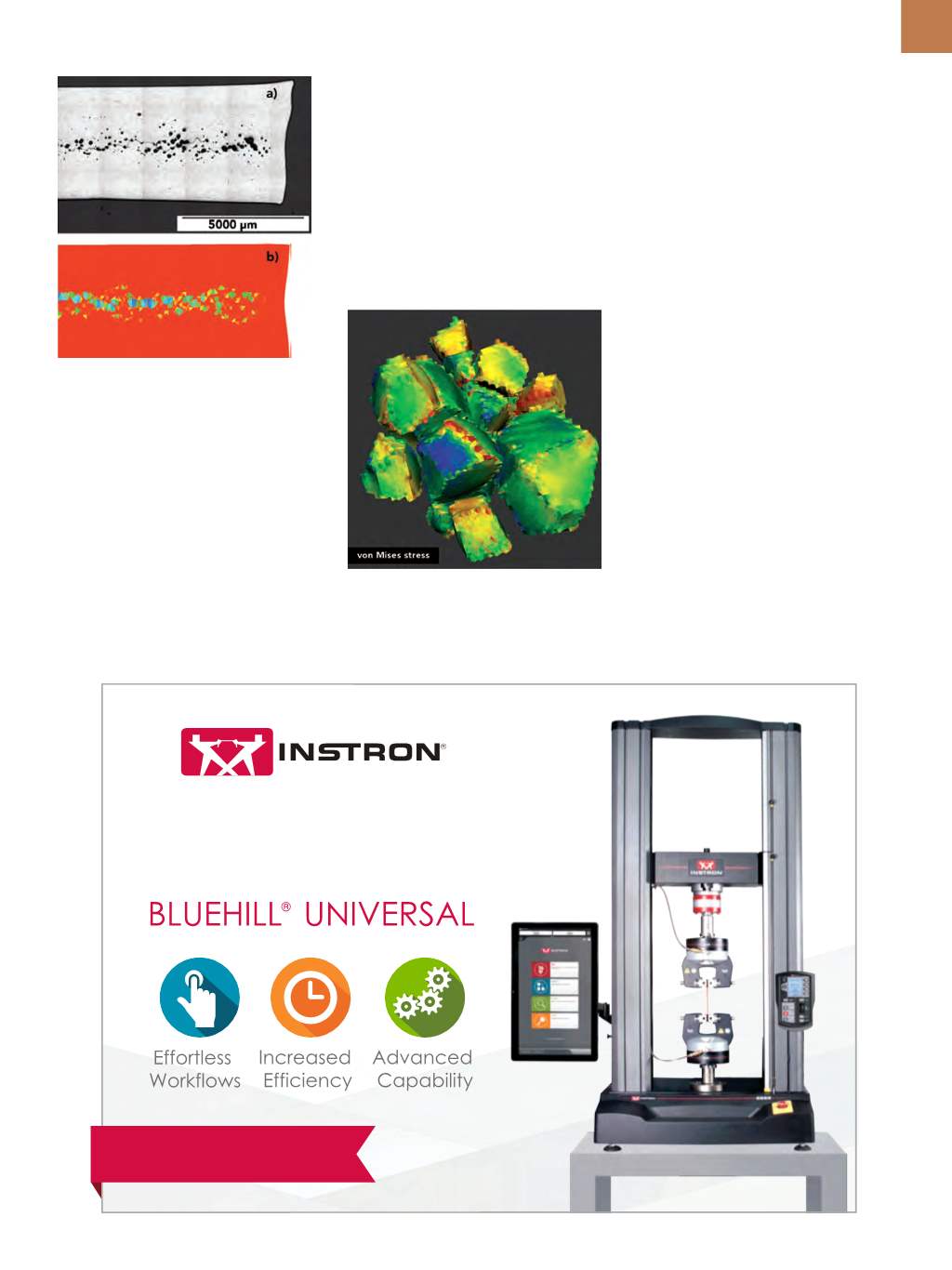
A D V A N C E D
M A T E R I A L S
&
P R O C E S S E S | F E B R U A R Y / M A R C H
2 0 1 7
1 9
PREDICTIVE CAPABILITY FOR
MATERIALS RESPONSE
Material structuremust be evaluat-
ed as a statistically varying quantity for
multiscale modeling and simulations of
a material’s response to loading. Thus,
it is necessary to represent many in-
stances of material structure. Digitally
generated microstructures using the
method described here are ideal for this
purpose because they can be easily im-
plemented into the simulations.
Plate impact experiments on tan-
talum produced a pattern of voids simi-
lar to that shown in Fig. 6(a). Figure 6(b)
shows that macroscale simulations of
the experiments replicate characteristic
features of the voids using constitutive
material models. However, these lack
the underpinnings of polycrystalline
mechanics needed to support predic-
tive simulations of material response to
loading
[16]
.
Use of a rate-dependent macro-
scale damage model
[16, 17]
enabled es-
timating the time in the experiment at
which the macroscale model suggests
progression of pore growth begins.
Numerical representation of experi-
mental results provides an estimate
of the stress state in the sample at this
predicted time of void initiation. Calcu-
lated stress state can then be applied to
mesoscale models of statistically equiv-
alent material structures as discussed
previously. Polycrystal simulations of
tantalum under loading trajectories
that match those in the plate impact
spall plane provide first order quanti-
tative estimates of the von Mises stress
on grain surfaces in the polycrystal.
Figure 7 shows an expanded view of von
Mises stress on the surface of individual
crystallite grains when maximum prin-
ciple tensile stress is at its peak. The
single crystal model used in these cal-
culations is based on thermally activat-
ed motion of dislocations
[18]
.
Fig. 6 —
Void pattern in (a) recovered
specimen and (b) macroscale simulation
of the experiment.
Fig. 7 —
Expanded view of simulated von
Mises stress on grain surfaces in polycrys-
talline tantalum; stress hot spots tend to
appear on triple points.
CONTACT US FOR A DEMO go.instron.com/BluehillUniversalIntroducing the Next Generation
of Materials Testing Software