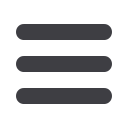
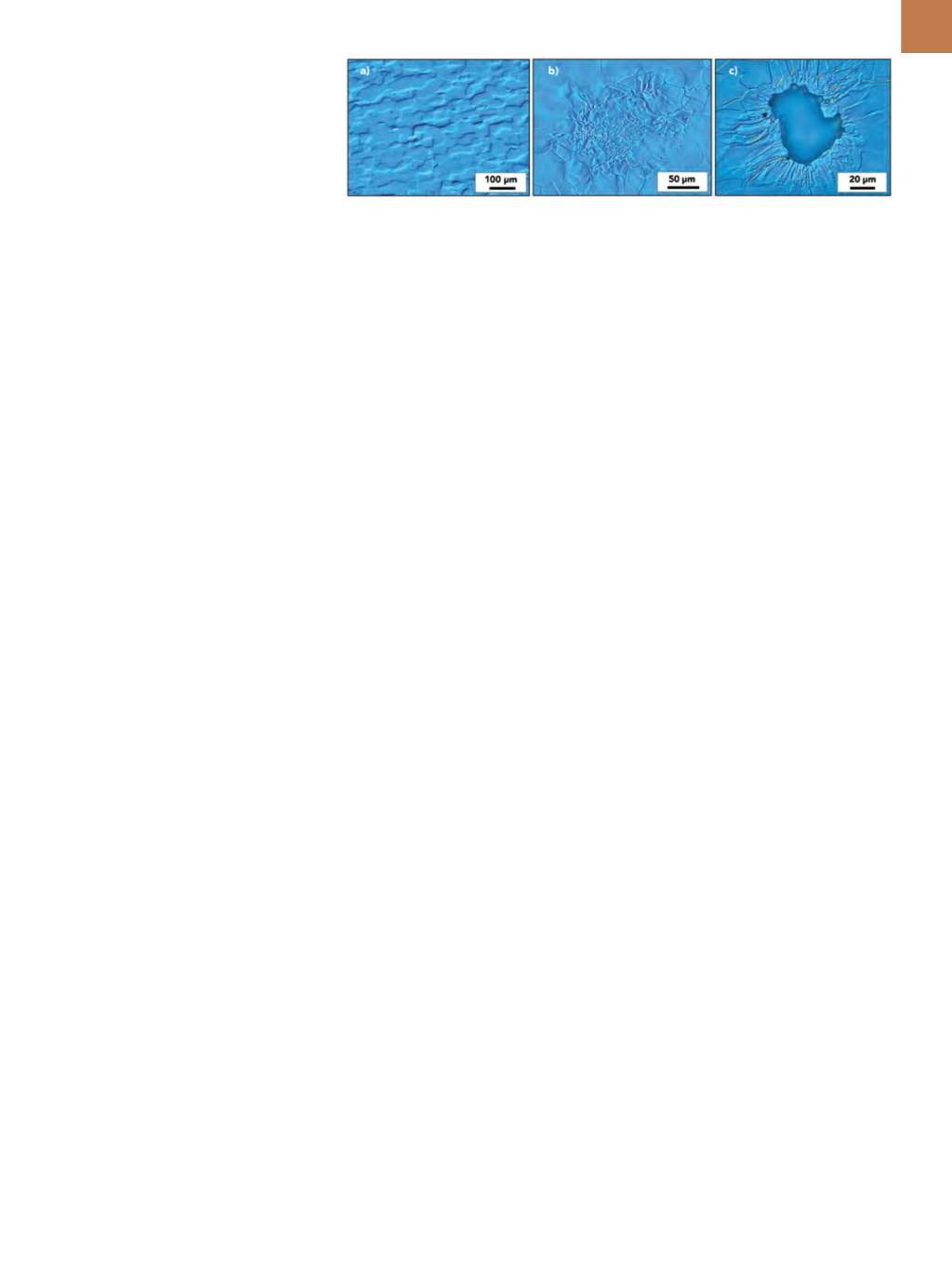
A D V A N C E D
M A T E R I A L S
&
P R O C E S S E S | F E B R U A R Y / M A R C H
2 0 1 7
1 7
description of microstructure in the
models.
Microscopy methods for unbiased
descriptions of microstructures have
undergone dramatic improvements.
The desire for 3D microstructural data
is relatively straightforward because
3D data provides access to important
geometrical and topological quantities
that cannot be determined or are erro-
neously quantified using classical stere-
ological methods applied to 2D images.
However, experimental 3D characteriza-
tion and quantification techniques still
require significantly more development
compared with conventional 2D analy-
sis. The state of the art for 3D materials
characterization is advancing and is
covered in the literature
[8-10]
. Depend-
ing on the area and features of inter-
est, different microscopy methods are
used to obtain 3D information. Meth-
ods used to obtain 3D statistics from
microstructures include stereology
[11]
,
serial sectioning with or without elec-
tron backscatter diffraction (EBSD)
[12]
to reconstruct microstructures in 3D,
3D FIB-SEM
[13]
, and high-energy diffrac-
tion microscopy
[14]
. However, because
it is not possible to measure all con-
ceivable microstructural features, char-
acterization must have a well-defined
scope.
LANL research on generating
digital materials models involves
DREAM.3D
[15]
, an open source software
package designed for the digital re-
construction, instantiation, quantifi-
cation, meshing, and visualization of
microstructures. This package allows
creation of synthetic microstructures
from automatically generated statistics
or from one’s own statistics. Recon-
structed volumes can be exported in
various formats, and statistical analysis
can be extracted for further use.
M
any challenges exist with regard
to understanding and represent-
ing complex physical processes
involved with ductile damage and fail-
ure in polycrystalline metallic materials.
Currently, the ability to accurately pre-
dict the macroscale ductile damage and
failure response of metallic materials
is lacking. Existing macroscale models
involve simple micromechanics of pore/
solid interactions, which do not take into
account microstructural effects. Recent
initiatives are driving greater interaction
between thematerials scienceanddesign
engineering communities as materials
research migrates to a science-based
capability to design materials for specific
applications. Such processing model
capabilities will predict the internal struc-
ture of materials under specific process-
ing conditions. Similarly, knowledge of
internal structures will enable materi-
als property models to predict material
performance under desired operating
conditions.
Past studies of the effect of mi-
crostructural and stress-state variables
on the evolution of damage show that
microstructure must not be neglect-
ed to enable predicting or avoiding
damage and failure. Other studies
show that physical processes of dam-
age nucleation and growth leading to
failure are substantially affected by
material anisotropy and the presence
of both intrinsic and extrinsic defects
and heterogeneities
[1-5]
. There is gen-
eral agreement that the mechanisms
of damage nucleation and growth un-
der mechanical loading strongly de-
pend on material processing and the
resulting microstructure
[6]
. However,
the underlying mechanisms and kinet-
ics controlling damage nucleation and
growth as a function of material micro-
structure and loading path are still not
well understood. The physics of ductile
damage and failure are approached
as an evolving process of nucleation,
growth, interaction, and coalescence,
which leads to failure. These stages
are observed experimentally in imag-
es captured using circular-differential
interference contrast (C-DIC) microsco-
py (Fig. 1). Unfortunately, these damage
and failure events cannot be predicted
without the use of mesoscale-aware
modeling tools. Crystal plasticity-based
simulations can predict the average
crystallographic texture and develop-
ment due to deformation, but cannot
predict the nature and extent of the lo-
cal intergranular misorientations due to
deformation
[7]
.
Research at Los Alamos National
Laboratory (LANL) is aimed at building
a coupled experimental and computa-
tional methodology that supports the
development of predictive damage
capabilities by:
•
Capturing real distributions of
microstructural features from real
material and implementing them as
digitally generated microstructures
in damage model development.
•
Distilling structure-property in-
formation to link microstructural
details to damage evolution under
a multitude of loading states.
MICROSTRUCTURE:
A3DCONCEPT
The internal structure of materials
is complex andmultiscale—and defined
by a large number of parameters. Micro-
structures of materials such as metals
are three-dimensional (3D). However,
most traditional methods developed to
study such materials depend on obser-
vations made in 2D sections due to their
opaque nature. Increasing demand for
modeling and simulation to predict ma-
terials properties and to provide more
realistic representations of microstruc-
tures have increased the need for high
accuracy characterization and analysis
of microstructures. Predictive represen-
tation of ductile damage and failure in
materials remains a significant compu-
tational challenge. Past quantification
efforts to characterize microstructural
aspects considered average quantities,
which in part were driven by the limited
Fig. 1 —
Stages in damage development observed experimentally in shocked tantalum:
(a) undeformed microstructure, (b) strain localization, and (c) void damage.