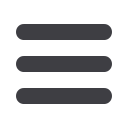
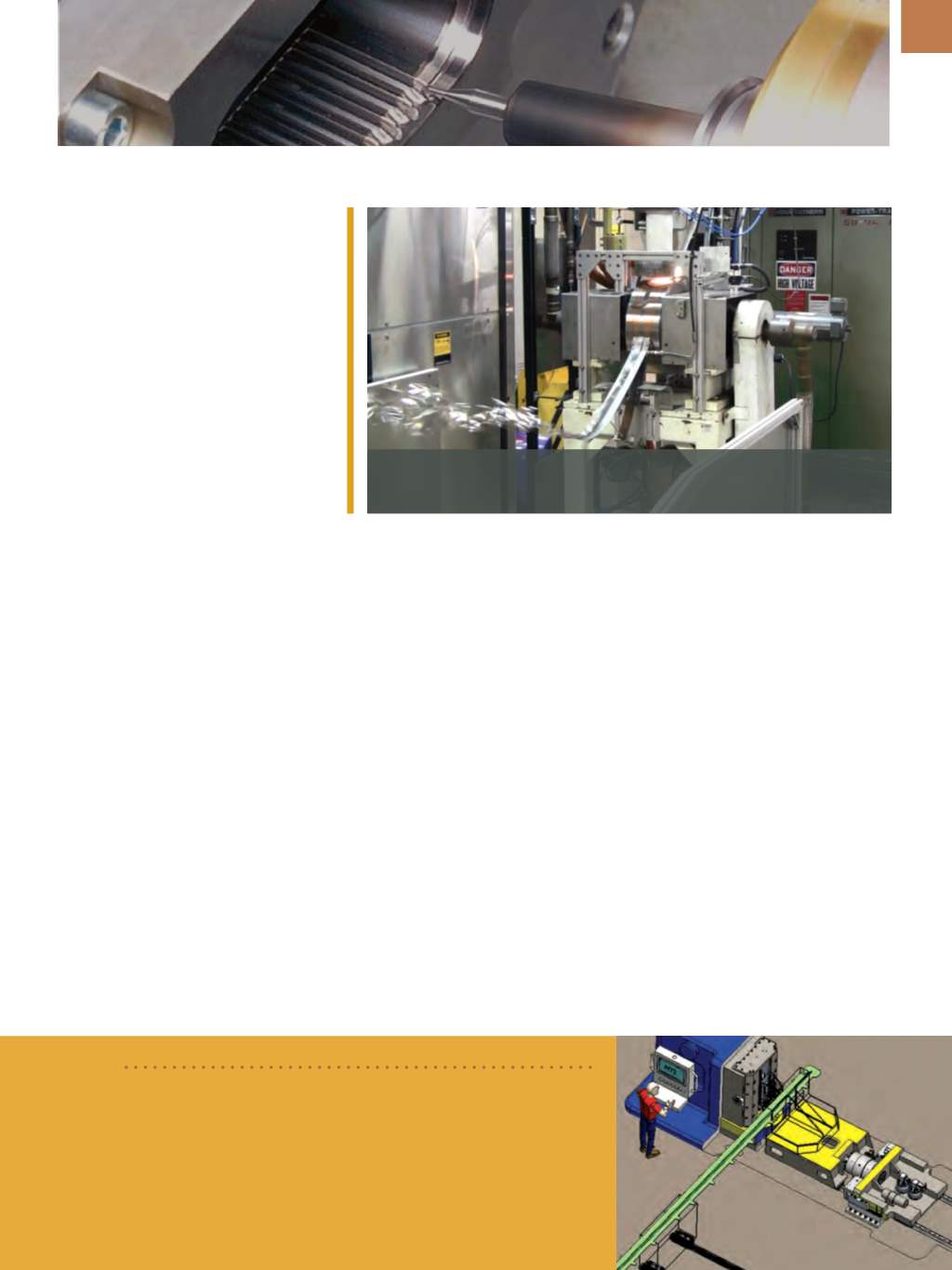
A D V A N C E D
M A T E R I A L S
&
P R O C E S S E S | F E B R U A R Y / M A R C H
2 0 1 7
1 3
A large-scale planar flow caster produces a custom soft alloy magnetic ribbon measuring
one mile long and up to 50 mmwide in NASA Glenn’s Magnetic Materials Fabrication and
Characterization Lab. Courtesy of NASA.
PROCESS TECHNOLOGY
Linear friction welder now in development.
Manufacturing Technology Inc.,
South Bend, Ind., is developing North America’s
largest linear friction welder—in terms of force capacity and tooling envelope—for
Lightweight Innovations for Tomorrow
(LIFT), Detroit, for use in automotive industry
research and development. The first of its kind in the U.S., the LF35-75 welder will be
housed in LIFT’s Corktown manufacturing center and is slated for completion in spring
2018.
mtiwelding.com.BRIEF
NASA GLENN INVITES
COLLABORATION
NASA’s Glenn Research Center,
Cleveland, acquired a large-scale pla-
nar flow caster at its Magnetic Material
Fabrication and Characterization Lab
that can produce custom soft alloy
magnetic ribbons measuring one mile
long and up to 50 mm wide. The caster
supports NASA’s hybrid electric aircraft
propulsion and power management
work, and is the largest in the nation for
conducting large-scale testing for com-
mercial use in a variety of fields.
Glenn’s Magnetic Material Fabri-
cation and Characterization Lab offers
fundamental alloy design, can produce
large quantities of customizedmaterial,
and can fabricate actual components,
making it a one-stop shop. In addition
to the large planar flow caster, a Bue-
hler 60-g caster capable of producing
approximately 25-mm-wide ribbons is
available for alloy development trials or
to produce smaller-scale components,
such as those on circuit boards. The lab
also offers an array of material charac-
terization equipment, including an al-
ternating current permeometer, vibrat-
ing sample magnetometer, permanent
magnet hysteresigraph, and a Magneto
Optical Kerr Effect microscope. The lab
welcomes collaboration with federal
entities, industry, academia, and other
groups.
For more information, contact
Randy Bowman at
randy.r.bowman@nasa.gov.
BELT CASTING BENEFITS
The Warwick Manufacturing Group
(WMG) at the University of Warwick, UK,
launched the ASSURE2 project to ex-
plore the potential of belt casting tech-
nology for steel production. As a near-
net shape casting process, belt casting
produces strip that needs minimal hot
deformation to achieve required prod-
uct thickness. Further, its use can min-
imize or eliminate the need for reheat-
ing processes—efficiencies that could
cut costs by more than 300% compared
to traditional continuous casting tech-
niques. In addition, belt casting could
be used to manufacture certain ad-
vanced high-strength strip steel grades
that are commercially attractive but
cannot be produced using conventional
casting, including TWIP (twinning in-
duced plasticity), TRIP (transformation
induced plasticity), and high-Al steels.
In their work so far, WMG research-
ers simulated belt cast microstructures,
including dynamic direct observation
of the solidifying steel at different cool-
ing rates. They demonstrated that mi-
crostructures are altered by the higher
cooling rate of belt casting compared
to slab casting and that further benefits
such as grain size reduction in high-Al
steels can be achieved by composition
control. Quantitative relationships be-
tween composition, process param-
eters, and microstructure are being
established, accounting for the higher
cooling rates of belt casting and re-
duced hot deformation after casting
to final thickness compared to conven-
tional processing. Eventually, trials at
the pilot plant facility at McGill Univer-
sity, Canada, will be undertaken for the
steel grades developed by ASSURE2.
www2.warwick.ac.uk.