
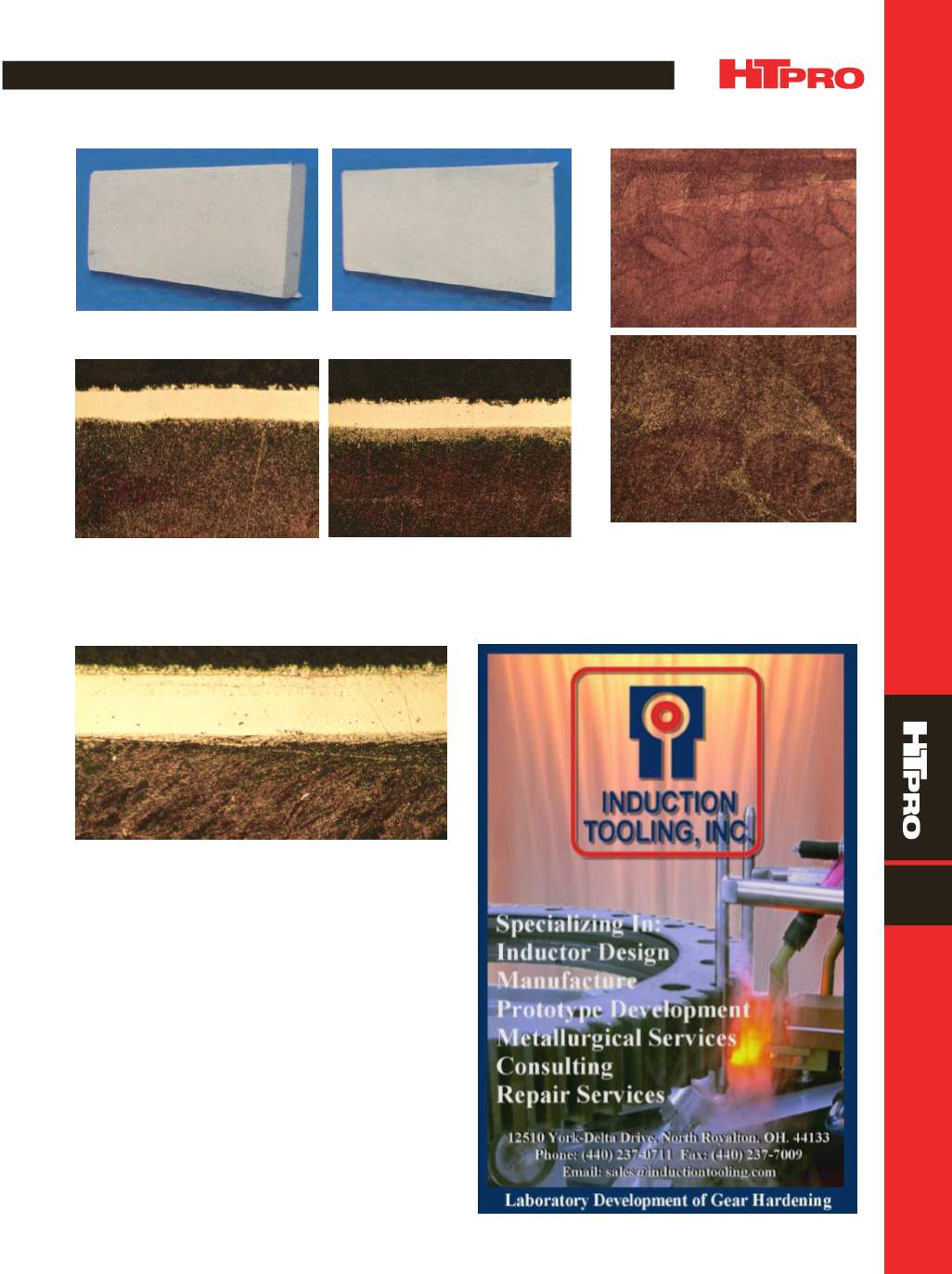
FEATURE
A D V A N C E D
M A T E R I A L S
&
P R O C E S S E S |
S E P T E M B E R
2 0 1 6
4 7
15
Fig. 3 —
Boronized surfaces: (a) unground and (b) ground.
Fig. 4 —
Boride layer on (a) ground and (b) as-printed surfaces. Boride layer depth
range: 0.0010-0.0011 in. Boride layer hardness (three locations): 2670, 2778, and 2892
HV (50 g load). Core hardness (four locations): 36.5, 39, 39, 39 HRC. Etchant: Marble’s
reagent. Original magnification 200
x
.
Fig. 5 —
Core microstructures. Etchant:
Marble’s reagent; (a) original magnifica-
tion 50
x
and (b) original magnification
200
x
.
COMPARING WROUGHT AND AM MATERIALS
A sample of Inconel 718 bar stock material was also
processed to compare results with those of the 3D-printed
material. Figure 6 shows the microstructure of the boride
layer on the bar stock test bar. It was concluded that boroniz-
ing of 3D-printed Inconel 718 is possible, and boride layer
depth, hardness, and microstructure are similar to results
for wrought Inconel 718.
For more information:
Craig Zimmerman is technical
director, Bluewater Thermal Solutions, 414.573.2832,
czimmerman@bluewaterthermal.com, www.bluewater-
thermal.com.
Fig. 6 —
Boride layer on wrought Inconel 718 test bar. Boride
layer depth range: 0.0012-0.0013 in. Boride layer hardness
(three locations): 3014, 2778, and 2892 HV (50 g load). Etchant:
Marble’s reagent. Original magnification 200x.
(a)
(b)
(a)
(b)
(a)
(b)